活性炭吸附塔生产过程***性和变形控制
活性炭吸附塔作为工业废气处理的核心设备,其生产过程需兼顾效率、安全性和长期稳定性。以下从生产过程***性与变形控制两方面展开分析:
一、生产过程***性
1. 材料选择与预处理
核心材料***性:活性炭吸附塔的效能依赖于活性炭的吸附性能,通常选用比表面积***(5001500m²/g)、孔隙结构发达的椰壳或煤质活性炭。根据废气成分(如VOCs、酸性气体、恶臭物质)选择专用炭种,例如电子行业需耐酸型活性炭,食品加工需符合FDA标准的食品级炭材。
预处理工艺:活性炭使用前需经过烘干、筛分等预处理,以避免水分堵塞微孔结构,影响吸附效率。
2. 塔体结构设计与制造
材质与防腐:塔体多采用304不锈钢或PP材质,腐蚀性环境可选钛合金或内衬防腐涂层。立式圆柱形结构(直径13m)可***化气流分布,降低阻力。
模块化生产:***型吸附塔采用分段式制造,现场焊接或法兰连接,确保密封性。多层抽屉式炭箱设计便于填料更换,延长维护周期。
3. 工艺流程与参数控制
吸附段设计:活性炭层厚度通常为300800mm,气流速度控制在0.30.6m/s,接触时间>1.5秒以保证吸附效率。
温度与压差监测:塔内设置温度传感器和压差计,实时监控吸附状态。当压差超过阈值(如500Pa)时,提示炭层饱和需再生。
4. 自动化与安全系统
温控与充氮保护:脱附再生时,高温(150300℃)可能导致活性炭自燃,需配备温度报警和充氮系统(氮气惰性化保护),避免火灾风险。
防爆设计:处理易燃易爆废气时,塔体需设置泄爆片和阻火器,并采用防爆型电气元件。
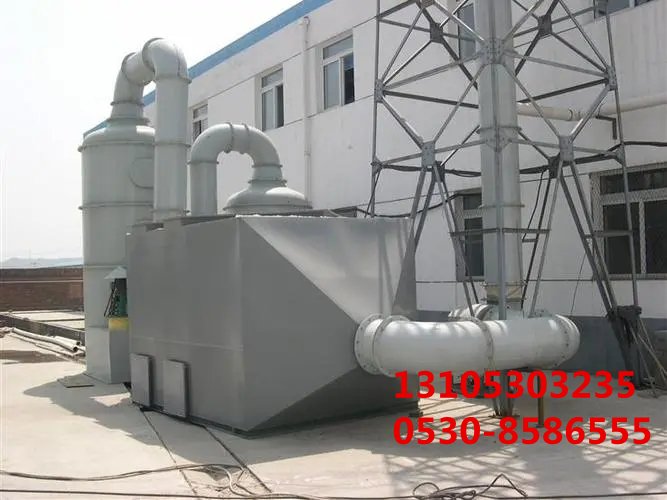
二、变形控制关键技术
1. 热应力变形控制
温度场均匀性***化:再生过程中,蒸汽或热风需均匀分布,避免局部过热。例如,通过旁路烟道引入净化后烟气预热活性炭,使脱硝区温度稳定在100150℃。
材料热膨胀补偿:塔体焊接时采用弹性接缝(如波形补偿器),吸收热胀冷缩产生的应力,防止焊缝开裂。
2. 机械负荷与压力变形
结构强化设计:塔体底部加强筋和支撑底座需承受活性炭层重量(密度约500kg/m³),并通过有限元分析***化受力分布。
压差平衡策略:吸附过程中,压差过***可能导致塔壁鼓包。通过调节风机频率或增设导流板,平衡各层炭床的气流分布。
3. 长期稳定性控制
沉降与磨损监测:定期检查炭层沉降情况(年损耗率515%),补充新鲜活性炭,避免因填料不均导致塔体倾斜。
防腐与疲劳防护:对金属塔体进行喷砂除锈和防腐涂装,周期性更换易损件(如分布器、密封圈),延长设备寿命。
三、行业应用与技术经济性
1. 典型场景适配
电子行业:处理PCB蚀刻废气(HCl、Cl₂),选用耐酸活性炭,配套碱液喷淋预处理。
喷涂车间:采用“吸附塔+催化燃烧”组合工艺,VOCs去除率>99%,炭层再生能耗降低60%。
2. 成本与效益
投资回收期:设备成本约占总投资的30%,通过节能运行(对比焚烧法省电60%)和模块化扩容,回收期通常<2年。
维护***化:智能化控制系统(如压差自动调节、远程监控)可减少人工干预,降低运维成本。
四、未来发展方向
1. 材料创新:开发高吸附容量(如分子印迹炭)、低阻力新型炭材,提升单位体积处理效率。
2. 智能控制:基于物联网的预测性维护系统,实时***化再生周期和气流参数。
3. 资源化利用:探索吸附后活性炭的再生技术(如微波脱附),实现炭资源循环利用。
活性炭吸附塔的生产过程需融合材料科学、流体力学和热力学原理,通过精细化设计与动态调控,平衡效能与变形风险。未来,随着环保标准的提升和技术迭代,吸附塔将向智能化、低能耗方向持续升级。